Jak powszechnie wiadomo, sterylizator to zamknięty zbiornik ciśnieniowy, zazwyczaj wykonany ze stali nierdzewnej lub węglowej. W Chinach w użyciu jest około 2,3 miliona zbiorników ciśnieniowych, wśród których korozja metali jest szczególnie powszechna, stając się główną przeszkodą i przyczyną awarii wpływających na długotrwałą, stabilną pracę zbiorników ciśnieniowych. Jako rodzaj zbiornika ciśnieniowego, sterylizator nie może być ignorowany pod względem produkcji, użytkowania, konserwacji i kontroli. Ze względu na złożony mechanizm korozji, formy i charakterystyka korozji metali różnią się pod wpływem materiałów, czynników środowiskowych i stanów naprężeń. Przyjrzyjmy się teraz kilku powszechnym zjawiskom korozji zbiorników ciśnieniowych:
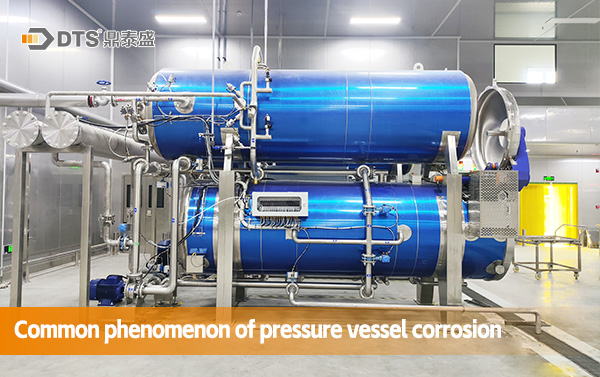
1. Korozja kompleksowa (znana również jako korozja równomierna), która jest zjawiskiem wywołanym korozją chemiczną lub elektrochemiczną. Medium korozyjne może równomiernie docierać do wszystkich części powierzchni metalu, dzięki czemu skład i struktura metalu są względnie jednorodne, a cała powierzchnia metalu ulega korozji w podobnym tempie. W przypadku zbiorników ciśnieniowych ze stali nierdzewnej, w środowisku korozyjnym o niskim pH, warstwa pasywacyjna może utracić swoje właściwości ochronne z powodu rozpuszczenia, co prowadzi do korozji kompleksowej. Niezależnie od tego, czy jest to korozja kompleksowa spowodowana korozją chemiczną, czy elektrochemiczną, wspólną cechą jest to, że trudno jest utworzyć ochronną warstwę pasywacyjną na powierzchni materiału podczas procesu korozji, a produkty korozji mogą rozpuścić się w medium lub utworzyć luźny porowaty tlenek, który nasila proces korozji. Szkodliwości korozji kompleksowej nie można lekceważyć: po pierwsze, prowadzi ona do zmniejszenia ciśnienia w obszarze nośnym zbiornika ciśnieniowego, co może spowodować przeciek perforacyjny, a nawet pęknięcie lub złom z powodu niewystarczającej wytrzymałości; Po drugie, w procesie elektrochemicznej korozji kompleksowej często zachodzi reakcja redukcji jonów H+, która może powodować wypełnienie materiału wodorem, a to z kolei prowadzi do kruchości wodorowej i innych problemów. Z tego też powodu sprzęt należy odwodorniać podczas konserwacji spawalniczej.
2. Korozja wżerowa to lokalne zjawisko korozyjne, które rozpoczyna się na powierzchni metalu i rozprzestrzenia się wewnątrz, tworząc niewielkie wżery korozyjne w kształcie otworów. W określonym środowisku, po pewnym czasie, na powierzchni metalu mogą pojawić się pojedyncze wytrawione otwory lub wżery korozyjne, które z czasem będą się pogłębiać. Chociaż początkowa utrata masy metalu może być niewielka, ze względu na szybkie tempo lokalnej korozji, ściany urządzeń i rur często ulegają perforacji, co prowadzi do nagłych wypadków. Kontrola korozji wżerowej jest trudna, ponieważ otwór wżerowy jest niewielki i często pokryty produktami korozji, przez co trudno jest ilościowo zmierzyć i porównać stopień korozji. Dlatego korozja wżerowa może być uważana za jedną z najbardziej destrukcyjnych i podstępnych form korozji.
3. Korozja międzykrystaliczna to lokalne zjawisko korozyjne występujące wzdłuż lub w pobliżu granicy ziaren, głównie ze względu na różnicę między powierzchnią ziarna a wewnętrznym składem chemicznym, a także obecność zanieczyszczeń na granicy ziaren lub naprężeń wewnętrznych. Chociaż korozja międzykrystaliczna może nie być widoczna na poziomie makro, po jej wystąpieniu wytrzymałość materiału maleje niemal natychmiast, często prowadząc do nagłej, nieoczekiwanej awarii urządzenia. Co gorsza, korozja międzykrystaliczna łatwo przekształca się w międzykrystaliczne pękanie korozyjne naprężeniowe, które staje się źródłem pękania korozyjnego naprężeniowego.
4. Korozja szczelinowa to zjawisko korozyjne występujące w wąskiej szczelinie (o szerokości zazwyczaj od 0,02 do 0,1 mm) utworzonej na powierzchni metalu z powodu ciał obcych lub przyczyn konstrukcyjnych. Szczeliny te muszą być wystarczająco wąskie, aby umożliwić przepływ cieczy i jej zatrzymanie, zapewniając w ten sposób warunki do korozji szczeliny. W zastosowaniach praktycznych, połączenia kołnierzowe, powierzchnie zagęszczające nakrętki, połączenia zakładkowe, nieprzespawane szwy spawalnicze, pęknięcia, pory powierzchniowe, nieoczyszczony żużel spawalniczy osadzający się na powierzchni metalu, zanieczyszczenia itp. mogą tworzyć szczeliny, powodując korozję szczelinową. Ta forma lokalnej korozji jest powszechna i wysoce destrukcyjna, i może uszkodzić integralność połączeń mechanicznych i szczelność urządzeń, prowadząc do awarii urządzeń, a nawet wypadków niszczących. Dlatego zapobieganie korozji szczelinowej i jej kontrola są bardzo ważne, a regularna konserwacja i czyszczenie urządzeń są wymagane.
5. Korozja naprężeniowa stanowi 49% wszystkich rodzajów korozji wszystkich zbiorników, charakteryzując się synergistycznym działaniem naprężeń kierunkowych i czynnika korozyjnego, prowadzącym do kruchego pękania. Ten rodzaj pęknięcia może rozwijać się nie tylko wzdłuż granicy ziaren, ale także przez samo ziarno. Głębokie pękanie wewnątrz metalu prowadzi do znacznego spadku wytrzymałości konstrukcji, a nawet do nagłego, nieoczekiwanego uszkodzenia metalowych urządzeń. Dlatego pękanie wywołane korozją naprężeniową (SCC) charakteryzuje się nagłym i silnym działaniem niszczącym. Po utworzeniu się pęknięcia jego tempo rozszerzania się jest bardzo szybkie i nie ma wyraźnego ostrzeżenia przed awarią, co jest bardzo szkodliwą formą awarii urządzeń.
6. Ostatnim powszechnym zjawiskiem korozji jest korozja zmęczeniowa, która odnosi się do procesu stopniowego uszkadzania powierzchni materiału, aż do jego pęknięcia pod wpływem łącznego działania naprężeń przemiennych i czynnika korozyjnego. Połączenie korozji i odkształceń przemiennych materiału powoduje wyraźne skrócenie czasu inicjacji i cyklu pęknięć zmęczeniowych, a także wzrost prędkości propagacji pęknięć, co powoduje znaczne obniżenie wytrzymałości zmęczeniowej materiałów metalowych. Zjawisko to nie tylko przyspiesza wczesną awarię elementu ciśnieniowego urządzenia, ale także znacznie skraca żywotność zbiornika ciśnieniowego zaprojektowanego zgodnie z kryteriami zmęczeniowymi. W trakcie użytkowania, aby zapobiec różnym zjawiskom korozji, takim jak korozja zmęczeniowa zbiorników ciśnieniowych ze stali nierdzewnej, należy podjąć następujące działania: co 6 miesięcy dokładnie czyścić wnętrze zbiornika sterylizacyjnego, zbiornika ciepłej wody i innych urządzeń; jeśli twardość wody jest wysoka i urządzenie jest używane dłużej niż 8 godzin dziennie, należy je czyścić co 3 miesiące.
Czas publikacji: 19-11-2024